WHY CHOOSE
TIME REDUCTION | HIGH PERFORMANCE | ECOLOGICAL
Is a true REVOLUTION in the traditional solid steel copper welding wires for MIG/MAG welding. The new BRONZE COATED guarantees high standard quality levels as the traditional coppered coated wires…
PLUS multiple advantages compared to other MIG/MAG welding products.
Deep studies, research, testing and investments in human resources, grave life to this new range of wires.
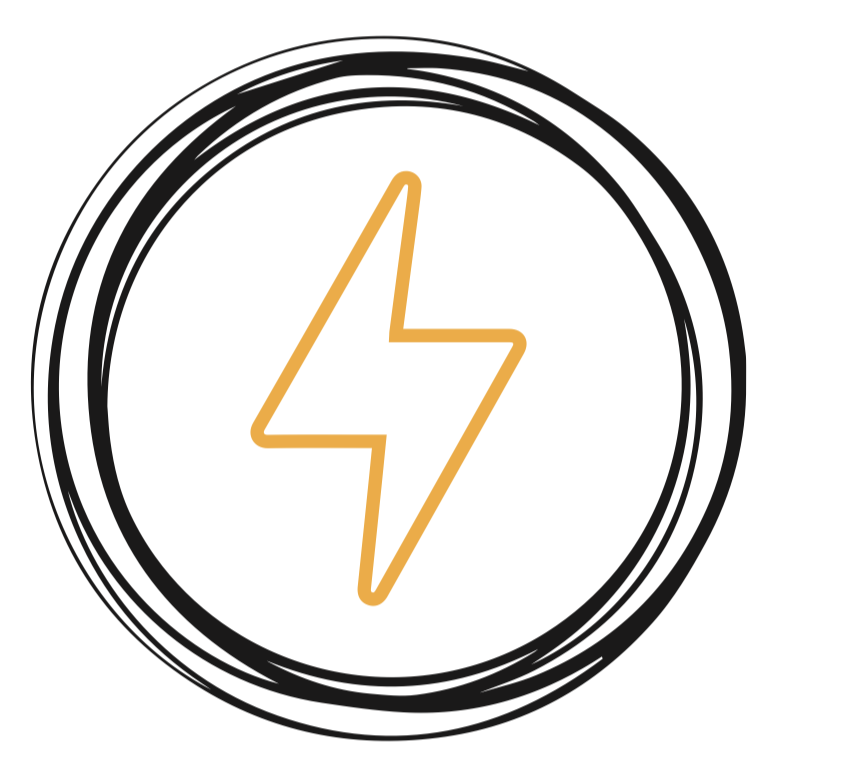
HIGH POWER DENSITY
The special coating combined with the action of a particular concentrations of the alloying elements of steel base, allow a weldability process of the BRONZE wires with power density up to 25-30% over standard parameters required by copper coated wires.
PERFECT STABILITY
OF THE ARC
The special production process and the lower amount of copper on the Bronze wire surface, allows minimum spattering actually possible in an automatic welding ensuring a great welding process cycle ;the feeding and the sliding of the wire is constant and this allows for a more stable welding arc, with a considerable cut in maintenance and down time. The start is immediate and the arc stabilizes in a shorter time compared to the best quality copper coated wires available in the market today.
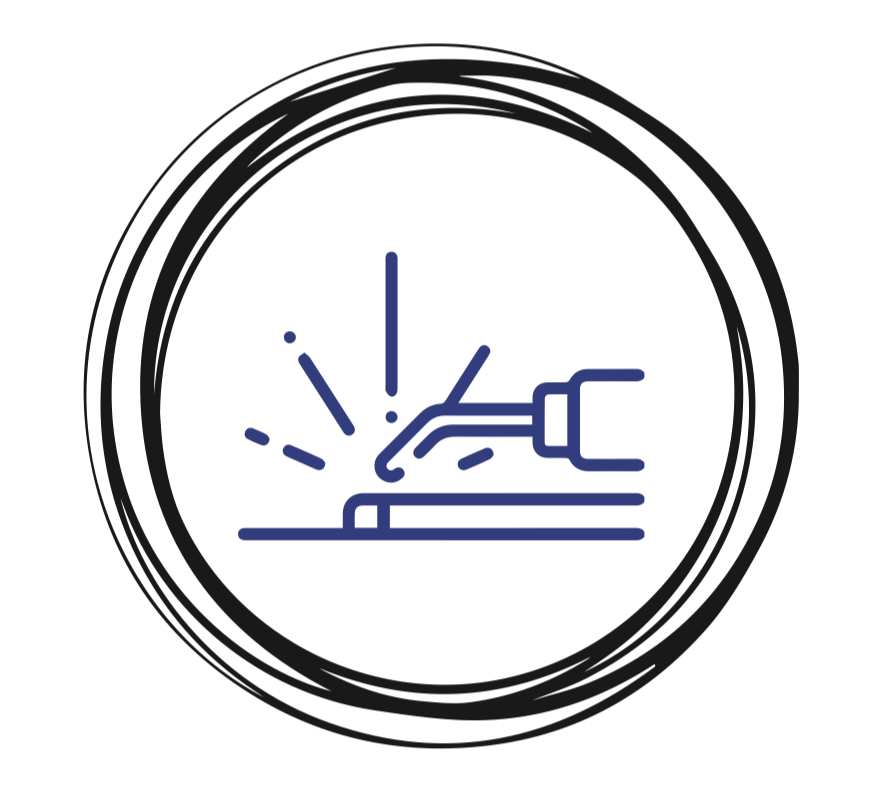
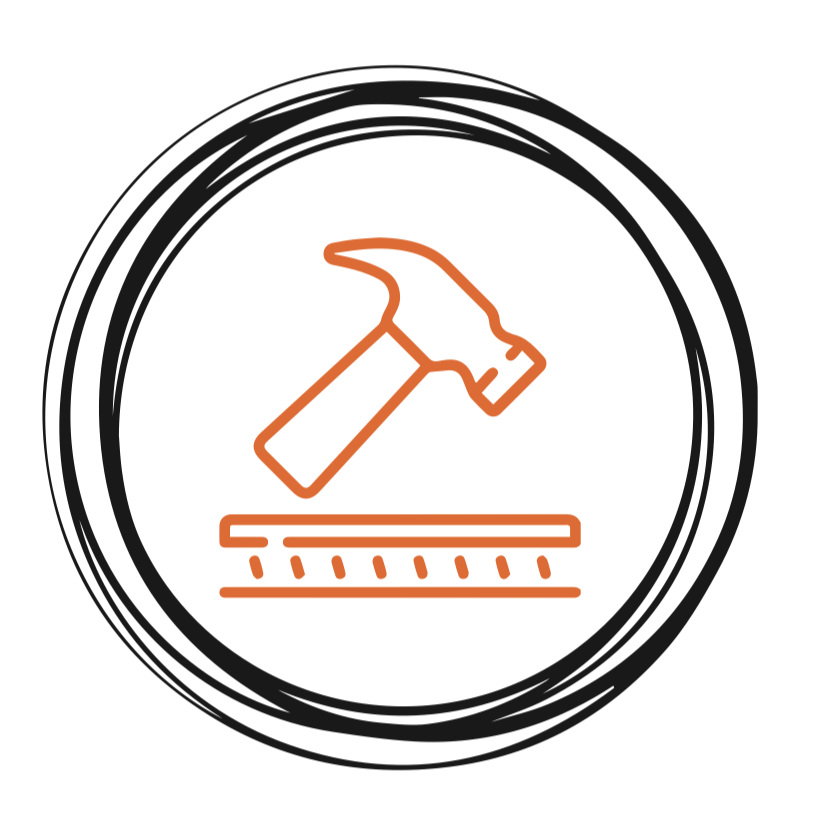
CLEANER WELD RESULT
AND LONG RESISTANCE
AGAINST CORROSION
The stick-out remains constant avoiding that, in the long run, the wire sticks to the nozzle and therefore entails the stop of the along with the considerable reduction of the silicates, complete the advantages of this unique and extraordinary wire.
LESS FUMES
We can now turn to the ecological aspect. Tests were carried out with the purpose to compare two wires of the same diameter produced from the same heat/lot number with the only difference in the type of surface coating, one with the classic copper coating and the other with BRONZE COATED. As for result we have a reduction in the rate of emission of fumes (FER) from the COPPER emission of copper going from 0,373 mg to 0,095 mg
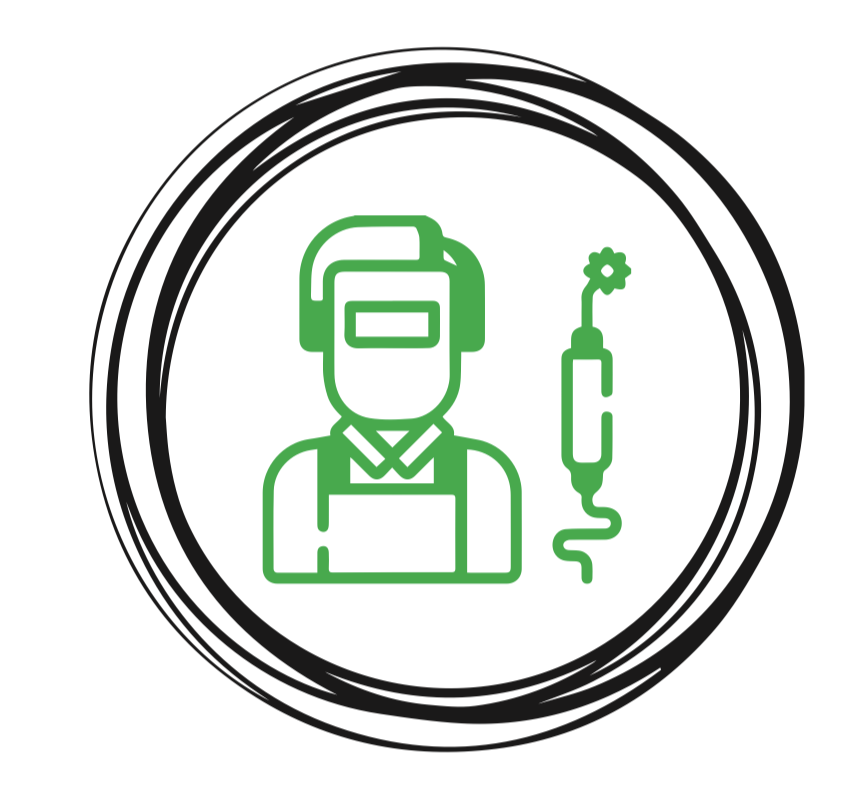